High Performance Computing with Productive Machines

As impressive as this may sound, it is natural to ask why this matters and how it can relate to optimising feeds and speeds. This is a great question and the one I am going to attempt to answer before explaining how Productive Machines can help use this computational power to reduce cycle times and eliminate chatter vibrations for milling operations.
Here at Productive Machines, we model tool/workpiece engagement at a very high resolution, both on the tool's surface and across the entire toolpath. We then take the model and simulate the cutting forces and resulting vibrations in unparalleled detail. This requires computing millions of calculations and gives us a unique view of the interaction between tool and workpiece. We input the results into our feed rate and spindle speed optimizers to provide users with the best possible toolpaths. This detailed understanding of the process also means we can remove the complexity involved in tuning and configuring the optimizers, further lowering the barrier to entry.
We use high performance computing to carry out these calculations in parallel, reducing the time users have to wait for the optimised toolpaths to a matter of minutes or hours. It is possible to optimise an entire part with many hundreds of operations in only the time it takes to optimise the longest path as we deploy an increasing amount of compute as you request more operations. We add even more parallel computing power by using many cores to calculate each toolpath optimisation, reducing the time to solution and allowing machinists to start cutting metal as fast as possible, without the need for costly iterations to find that optimal set of feeds and speeds.
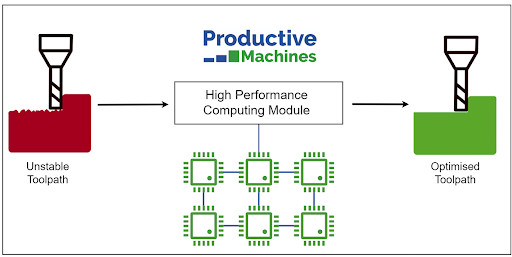
At this point, you may be wondering if this is simply too expensive or complex for you to be able to take advantage of. The good news is that we will worry about that! There is no need to procure new computing facilities or hire the teams responsible for operating and maintaining such systems. Using the optimisation services that Productive Machines offer means that CAM engineers and their workstations are free to move on to other tasks or parts while we do the hard work for them. Our CAM add ons, currently available for Siemens NX and MasterCAM, connect seamlessly to our service, so you can be up and running over a coffee break.
A further advantage of our software platform is that we can provide a continuous stream of new features and updates without forcing engineers to wait for annual releases. We are constantly working to improve on our already industry leading capabilities, and as soon as something is ready, it gets deployed automatically to benefit customers.
In order to deliver this service, we use data centres in the London area operated with the following certifications ISO/IEC 27001:2022, 27017:2015, 27018:2019, 27701:2019, 22301:2019, 20000-1:2018, 9001:2015, and CSA STAR CCM v4.0 by Amazon Web Services.
We understand that there are manufacturers who wish to use their own computing infrastructure and can offer an on premise solution for that scenario.